Low maintenance Overland Conveyor Rollers made to reduce power consumption by using Composite Rollers.
Overland conveyor rollers play a critical role in the operation of overland conveyors.
By selecting the right materials and design, overland conveyor rollers can be made to reduce power consumption, minimize maintenance, and extend the life of the conveyor.
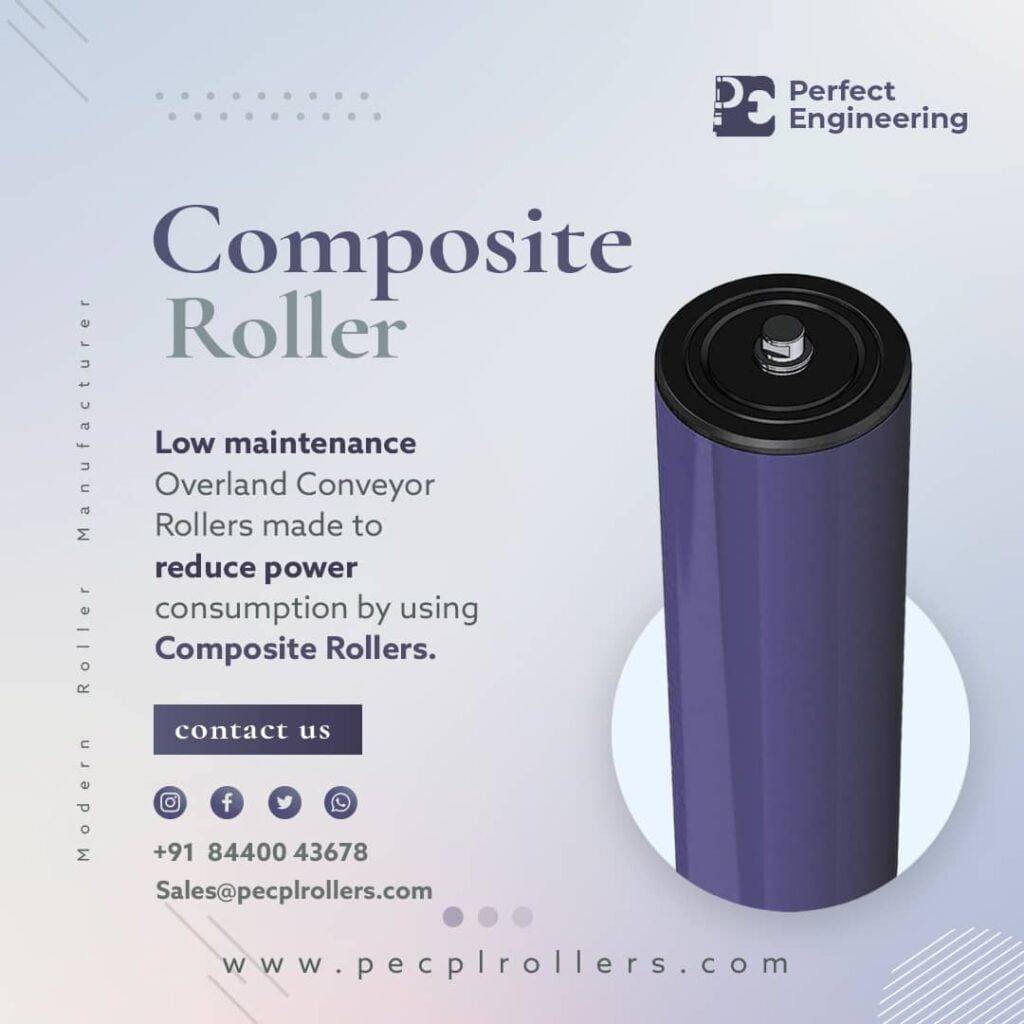
There are a number of factors to consider when selecting the right materials for overland conveyor rollers. The type of material used will have a direct impact on the roller’s ability to resist wear and tear. Harder materials, such as composites, will typically last longer and require less maintenance than softer materials. In addition, the material used should be able to withstand the environment in which it will be used.
For example, if the conveyor will be used in a corrosive environment, a material that is resistant to corrosion should be used. Once the right material has been selected, the next step is to select the right design for the overland conveyor rollers.
The design of the roller should take into account the weight of the material to be conveyed, the speed of the conveyor, and the width of the conveyor belt. By careful selection of the roller diameter, the roller can be made to minimize the power consumption of the conveyor.
In addition, the choice of roller material and design can have a significant impact on the life of the conveyor. For example, using a composite roller in a high-speed application may help to extend the life of the conveyor by reducing the friction between the roller and the conveyor belt.
Overland conveyor rollers are an important part of any overland conveyor system. By selecting the right materials and design, overland conveyor rollers can be made to reduce power consumption, minimize maintenance, and extend the life of the conveyor.There are a number of factors to consider when selecting the right materials for overland conveyor rollers.
The type of material used will have a direct impact on the roller’s ability to resist wear and tear. Harder materials, such as composites, will typically last longer and require less maintenance than softer materials. In addition, the material used should be able to withstand the environment in which it will be used. For example, if the conveyor will be used in a corrosive environment, a material that is resistant to corrosion should be used. Once the right material has been selected, the next step is to select the right design for the overland conveyor rollers.
The design of the roller should take into account the weight of the material to be conveyed, the speed of the conveyor, and the width of the conveyor belt. By careful selection of the roller diameter, the roller can be made to minimize the power consumption of the conveyor. In addition, the choice of roller material and design can have a significant impact on the life of the conveyor.
For example, using a composite roller in a high-speed application may help to extend the life of the conveyor by reducing the friction between the roller and the conveyor belt.